Volkswagen Tiguan Reparaturanleitung: Ventiltrieb
Montageübersicht - Ventiltrieb
Vorsicht!
Beschädigungsgefahr von Ventilen und Kolbenböden nach Arbeiten am
Ventiltrieb.
- Weil sich die hydraulischen Ausgleichselemente setzen müssen, darf der
Motor nach dem Einbau der Nockenwellen etwa 30 Minuten nicht gestartet
werden.
- Um sicherzustellen, dass kein Ventil beim Anlassen aufsetzt, Kurbelwelle
vorsichtig mindestens 2 Umdrehungen durchdrehen.
Hinweis
Zylinderköpfe mit Rissen zwischen den Ventilsitzen können ohne Herabsetzung
der Lebensdauer weiterverwendet werden, wenn es sich um leichte, maximal 0,5 mm
breite Anrisse handelt.
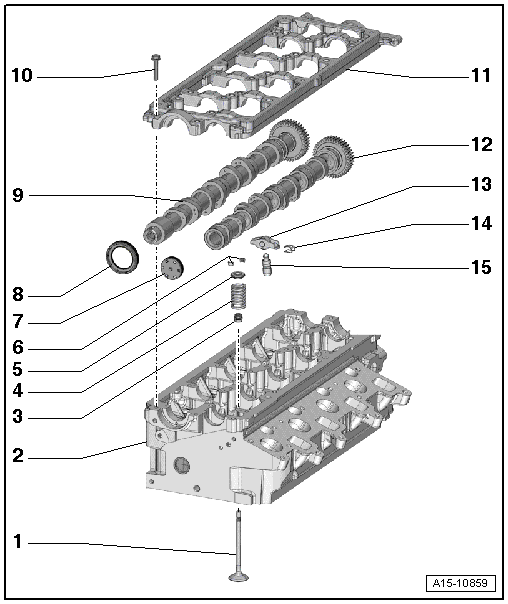
- Ventil
- nicht nacharbeiten, nur Einschleifen ist zulässig
- für den Wiedereinbau Einbaulage kennzeichnen
- prüfen
- Ventilmaße
- Ventilführungen prüfen
- Zylinderkopf
- Ventilschaftabdichtung
- ersetzen bei eingebautem Zylinderkopf ,
- ersetzen bei ausgebautem Zylinderkopf
- Ventilfeder
- Ventilfederteller
- Ventilkegelstücke
- Verschlussdeckel
- ersetzen
- ausbauen: Bei eingebautem Leiterrahmen mit einem Vorstecher an einer
Seite des Deckels einstechen und aushebeln
- einbauen: Ohne Dichtmittel mit passendem Druckstück eintreiben
- Eintreibtiefe 1 ... 2 mm
- Wellendichtring
- Auslassnockenwelle
- aus- und einbauen
- Axialspiel messen
- Radialspiel messen
- Schraube
- Anzugsdrehmoment und -reihenfolge
- Leiterrahmen
- mit integrierten Nockenwellenlagern
- Anzugsdrehmoment und -reihenfolge
- Einlassnockenwelle
- aus- und einbauen
- Axialspiel messen
- Radialspiel messen
- Rollenschlepphebel
- für den Wiedereinbau Einbaulage kennzeichnen
- Rollenlager auf leichten Lauf prüfen
- vor dem Einbauen Laufflächen ölen
- Sicherungsklammer
- für hydraulisches Ausgleichselement
- Hydraulisches Ausgleichselement
- für den Wiedereinbau Einbaulage kennzeichnen
- vor dem Einbauen Laufflächen ölen
Leiterrahmen - Anzugsdrehmoment und -reihenfolge
- Schrauben in 2 Stufen in der gezeigten Reihenfolge festziehen:
Stufe |
Schrauben |
Anzugsdrehmoment |
1. |
-1 ... 24- |
von Hand bis zur Anlage
eindrehen
- Der Leiterrahmen muss mit der gesamten Anlagefläche auf dem
Zylinderkopf aufliegen
|
2. |
-1 ... 24- |
10 Nm |
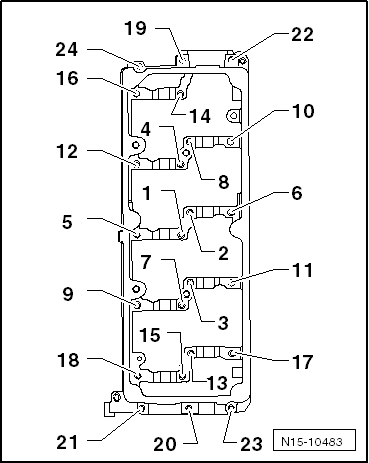
Axialspiel der Nockenwelle messen
Benötigte Spezialwerkzeuge, Prüf- und Messgeräte sowie Hilfsmittel
- Universal-Messuhrhalter -VW 387-
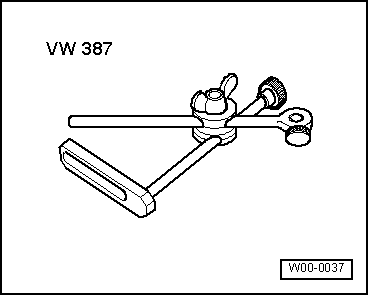
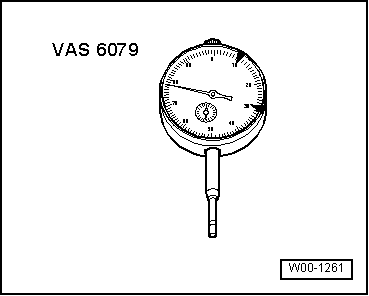
Arbeitsablauf
- Leiterrahmen ausbauen.
- Messuhr -VAS 6079- mit Universal-Messuhrhalter -VW 387- am Zylinderkopf
befestigen, wie in der Abbildung dargestellt.
- Nockenwelle von Hand gegen die Messuhr drücken.
- Messuhr auf "0" stellen.
- Nockenwelle von Messuhr abdrücken und Wert ablesen:
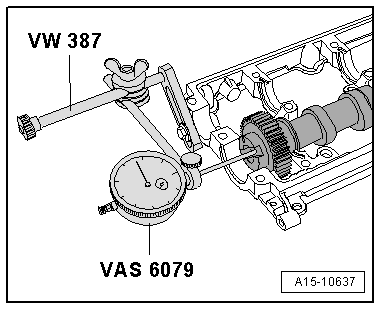
Axialspiel Einlass- und Auslassnockenwelle:
- Sollwert: 0,048 ... 0,118 mm.
- Verschleißgrenze 0,17 mm.
Radialspiel der Nockenwelle messen
Benötigte Spezialwerkzeuge, Prüf- und Messgeräte sowie Hilfsmittel
Arbeitsablauf
- Rollenschlepphebel ausbauen.
- Lager und Lagerzapfen reinigen.
- Plastigage der Lagerbreite entsprechend auf den zu messenden Lagerzapfen
oder in die Lager legen.
- Der Plastigage muss in der Mitte des Lagers liegen.
- Leiterrahmen aufsetzen und mit 10 Nm festziehen, dabei Nockenwellen
nicht verdrehen.
- Leiterrahmen wieder ausbauen.
- Breite des Plastigage mit der Messskala vergleichen
- Radialspiel: 0,035 ... 0,085 mm.
Nockenwelle aus- und einbauen
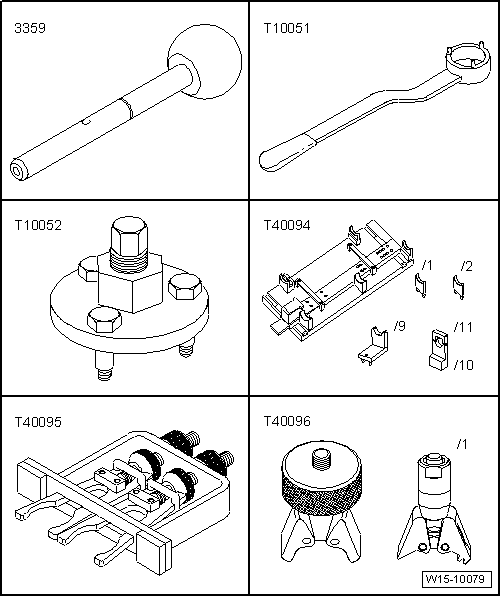
Benötigte Spezialwerkzeuge, Prüf- und Messgeräte sowie Hilfsmittel
- Absteckstift für Diesel-Einspritzpumpe -3359-
- Gegenhalter -T10051-
- Abziehvorrichtung -T10052-
- Nockenwellen-Einlegewerkzeug -T40094-
- Nockenwellen-Klemmwerkzeug -T40095-
- Nockenwellen-Spannwerkzeug -T40096-
- Drehmomentschlüssel -V.A.G 1331/-
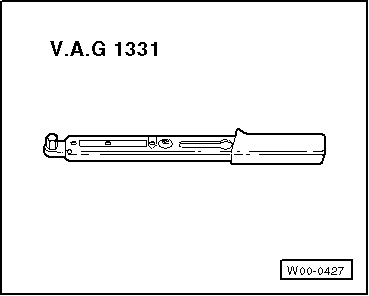
- Drehmomentschlüssel -V.A.G 1332/-
- Silikon-Klebedichtmittel -D 176501 A1-
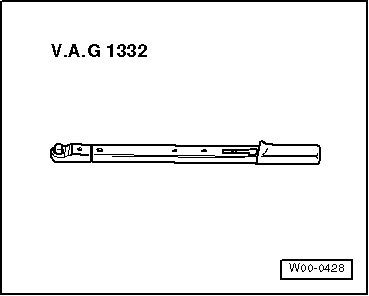
Ausbauen
- Motorabdeckung abbauen
- Kraftstofffilter ausbauen
- Wenn verbaut, die Zusatzkraftstoffpumpe -V393- bzw. die Kraftstoffpumpe
2 -V277- ausbauen
- Zahnriemen von Nockenwelle und Hochdruckpumpe abnehmen
- Zylinderkopfhaube abbauen
- Befestigungsschrauben -1- des
Nockenwellenrads herausschrauben.
- Nockenwellenrad von der Nabe abnehmen.
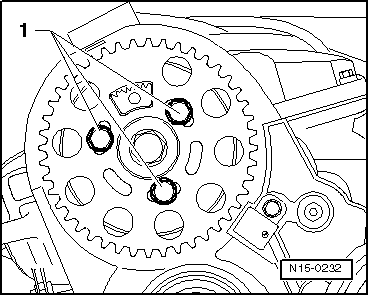
- Nabe mit dem Gegenhalter -T10051- gegenhalten und die
Befestigungsschraube -1- der Nabe lösen.
- Befestigungsschraube der Nabe ca. 2 Umdrehungen herausdrehen.
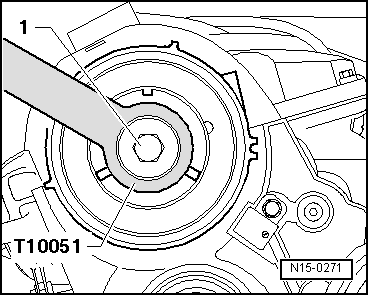
- Abziehvorrichtung -T10052- ansetzen und zu den Bohrungen der Nabe
ausrichten.
- Befestigungsschrauben -1- festziehen.
- Nabe durch gleichmäßiges Anziehen der Abziehvorrichtung
-2- unter Spannung setzen, bis sich die Nabe
vom Konus der Nockenwelle löst.
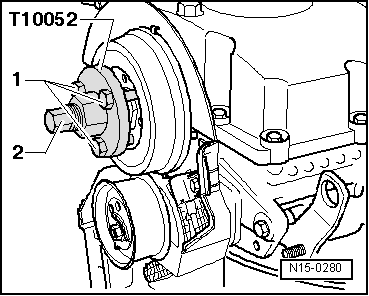
Hinweis
Abziehvorrichtung mit einem Schraubenschlüssel Schlüsselweite 30 festhalten.
- Nabe vom Konus der Nockenwelle abnehmen.
- Unterdruckpumpe ausbauen
- Befestigungsschrauben des Lagerrahmens in der Reihenfolge
-24 ... 1- herausdrehen.
- Lagerrahmen abnehmen.
- Nockenwellen vorsichtig herausnehmen.
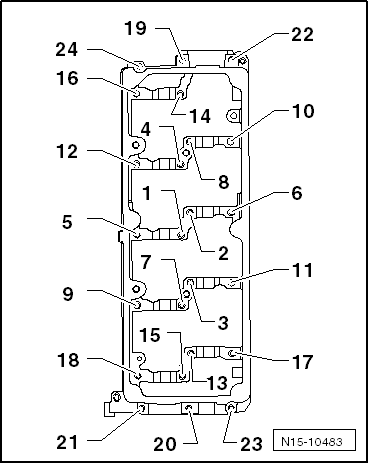
Hinweis
Trennfläche zwischen Lagerrahmen und Zylinderkopf mit
Silikon-Klebedichtmittel -D 176 501 A1- abdichten.
Vorsicht!
Die Nockenwellen dürfen nur, wie nachfolgend beschrieben, mit dem
Nockenwellen-Einlegewerkzeug -T40094- eingebaut werden. Es werden sonst die
Axiallager im Lagerrahmen zerstört und der Zylinderkopf ersetzt werden muss.
- Dichtmittelreste am Zylinderkopf und am Lagerrahmen z. B. mit
rotierender Kunststoffbürste entfernen.
Vorsicht!
Darauf achten, dass keine Dichtmittelreste in den Zylinderkopf bzw. die Lager
gelangen.
- Dichtflächen, müssen öl- und fettfrei sein.
- Laufflächen der Nockenwellen ölen.
Falls noch nicht geschehen, das Nockenwellen-Einlegewerkzeug -T40094- für
Nockenwellen wie folgt aufrüsten:
- Aufnahmen -T40094/3-, -T40094/4- und
-T40094/5- von der Grundplatte abbauen.
Verschraubung von unten.
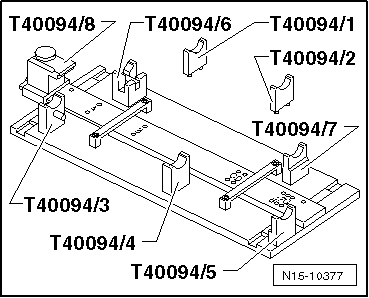
Hinweis
Sind die Aufnahmen Ihres Nockenwellen-Einlegewerkzeuges -T40094- noch nicht
gekennzeichnet, die demontierten Aufnahmen kennzeichnen, z. B. mit Schlagzahlen,
um eine spätere Zurückrüstung zu gewährleisten.
- Stattdessen die Aufnahmen -T40094/9- und
-T40094/10- auf die äußeren frei gewordenen
Positionen bauen.
- Aufnahme -T40094/2- auf die Position "A"
und die Aufnahme -T40094/1- auf die Position
"F" setzen.
- Zuerst die Einlassnockenwelle wie gezeigt einlegen. Darauf achten, dass
die Ausbuchtung -Pfeil- für die
Zylinderkopfschraube nach "außen" zeigt.
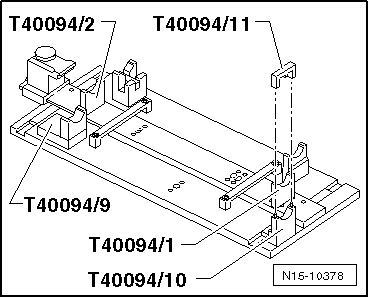
- Fühlerblattlehre 0,50 mm auflegen und die Aufnahme
-T40094/8- in die Nut der Einlassnockenwelle schieben.
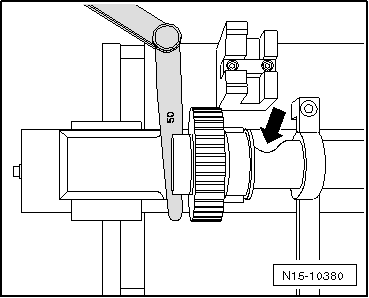
- Auslassnockenwelle einlegen und über deren Nut
-Pfeil- mit dem -Deckel T40094/11-
arretieren.
- Spannwerkzeug -T40096/1- auf die Zahnräder der Auslassnockenwelle
setzen.
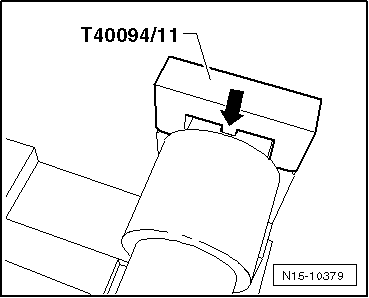
Vorsicht!
Darauf achten, dass die mit einem Pfeil gekennzeichnete Klemmbacke auf dem
breiteren Zahnrad sitzt.
- Spannwerkzeug -T40096/1- mit dem Rändelrad spannen, bis die Zahnflanken
in einer Flucht stehen. Einen Maulschlüssel Schlüsselweite 13 ggf. zu Hilfe
nehmen.
- Auslassnockenwelle zur Einlassnockenwelle schieben, bis die Verzahnungen
im Eingriff sind.
- Lagerrahmen auf die Nockenwellen auflegen.
- Alle Nockenwellenlager müssen auf den Nockenwellen aufliegen.
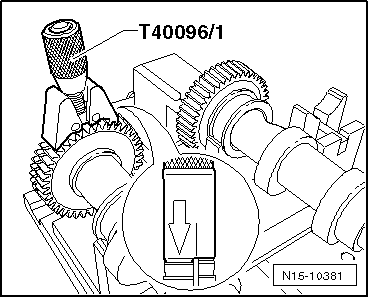
- Klemmwerkzeug -T40095- wie gezeigt aufsetzen und so die Nockenwellen im
Lagerrahmen fixieren.
- Deckel -T40094/11- abnehmen.
- Aufnahme -T40094/8- aus der Nut der Einlassnockenwelle ziehen.
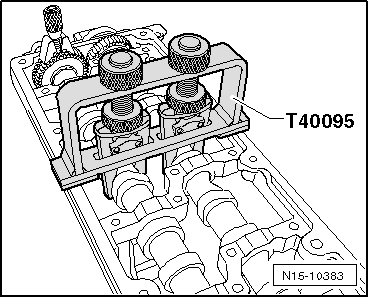
- Tubendüse an der vorderen Markierung abschneiden (Ø der Düse ca. 2 mm).
- Dichtmittelraupen (ca. 2 ... 3 mm breit) -Pfeile-,
wie in der Abb. gezeigt, auf die sauberen Dichtflächen des Zylinderkopfs
auftragen.
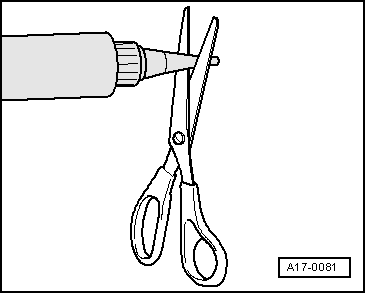
Vorsicht!
Verschmutzungsgefahr der Nockenwellenlager durch überschüssiges Dichtmittel
sowie Gefahr von Verschließen der Ölversorgungsbohrungen.
- Dichtmittelraupen nicht dicker als angegeben auftragen.
- Im Bereich der Ölversorgungsbohrungen -Pfeil-
für den Lagerrahmen darauf achten, dass diese nicht durch überschüssiges
Dichtmittel verschlossen werden.
Dichtmittelraupe für Lagerrahmen
- Nockenwellen zusammen mit dem Lagerrahmen und dem Klemmwerkzeug -T40095-
aus dem Nockenwellen-Einlegewerkzeug -T40094- herausnehmen.
- Nockenwellen und den Lagerrahmen vorsichtig in den Zylinderkopf
einlegen.
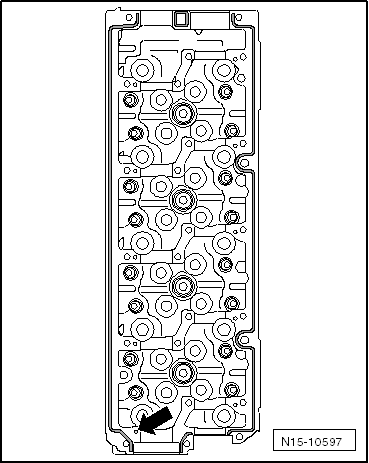
- Befestigungsschrauben des Lagerrahmens in der Reihenfolge
-1 ... 24- zunächst handfest anziehen.
- Der Leiterrahmen muss mit der gesamten Anlagefläche auf dem
Zylinderkopf aufliegen.
- Schrauben des Lagerrahmens in der Reihenfolge
-1 ... 24- auf Endanzug festziehen. Anzugsdrehmoment: 10 Nm
- Klemmwerkzeug -T40095- und das Spannwerkzeug -T40096/1- abnehmen.
- Nockenwellen-Dichtring ersetzen
- Einen neuen Verschlussdeckel am Zylinderkopf mit einem geeigneten Dorn
bündig eintreiben.
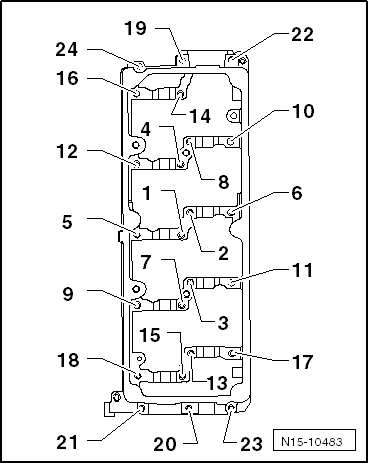
Der weitere Einbau erfolgt in umgekehrter Reihenfolge, dabei ist Folgendes zu
beachten:
Vorsicht!
Beschädigungsgefahr von Ventilen und Kolbenböden nach Arbeiten am
Ventiltrieb.
- Weil sich die hydraulischen Ausgleichselemente setzen müssen, darf
der Motor nach dem Einbau der Nockenwellen etwa 30 Minuten nicht
gestartet werden.
- Um sicherzustellen, dass kein Ventil beim Anlassen aufsetzt,
Kurbelwelle vorsichtig mindestens 2 Umdrehungen durchdrehen.
- Nabe auf die Nockenwelle setzen.
- Befestigungsschraube -1- der Nabe mit
100 Nm festziehen. Dazu den Gegenhalter -T10051- verwenden.
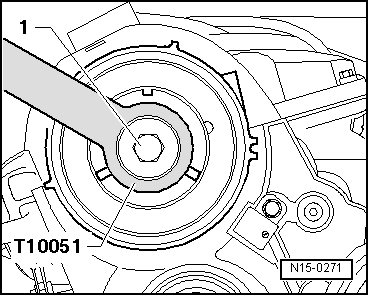
- Nockenwellenrad auf die Nabe schieben.
Hinweis
Das Zahnsegment -Pfeil- des Nockenwellenrads
muss oben stehen.
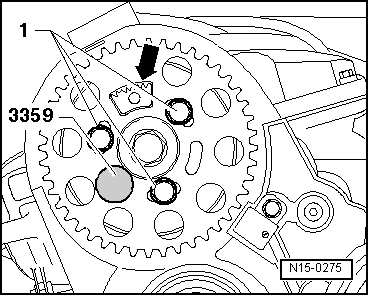
- Befestigungsschrauben -1- von Hand
spielfrei zum Nockenwellenrad ansetzen.
- Nabe mit dem Absteckstift -3359- arretieren.
- Zahnriemen einbauen und die Steuerzeiten einstellen
- Unterdruckpumpe einbauen
- Zylinderkopfhaube einbauen
- Kraftstofffilter einbauen
- Wenn verbaut, die Zusatzkraftstoffpumpe -V393- bzw. die Kraftstoffpumpe
2 -V277- einbauen
Nockenwellendichtring aus- und einbauen
Hinweis
Gleitend setzt ein neuer Dichtring -B- ein, der
visuell keine geschlossene Oberfläche zwischen Nockenwelle und Zylinderkopf mehr
bietet, sondern eher eine Hohlkehle erkennen lässt. Hier muss ein anderer
Arbeitsablauf durchgeführt werden.
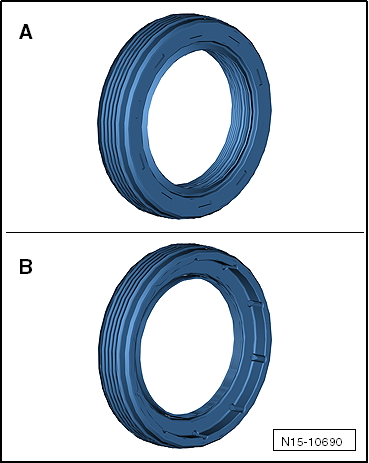
Fahrzeuge mit "altem" Dichtring
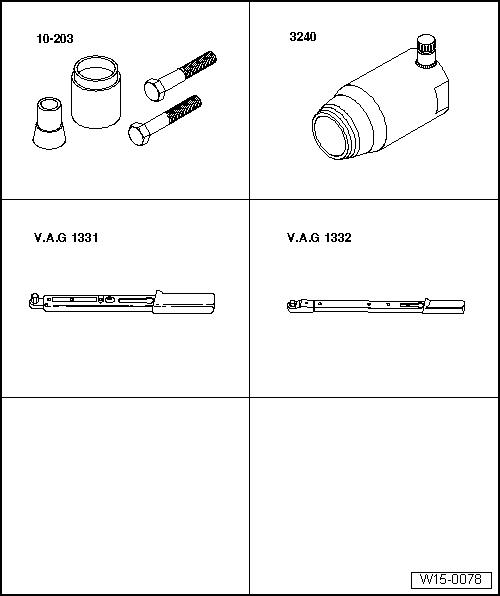
Benötigte Spezialwerkzeuge, Prüf- und Messgeräte sowie Hilfsmittel
- Einziehvorrichtung -V.A.G 10-203-
- Dichtringauszieher -3240-
- Drehmomentschlüssel -V.A.G 1331/-
- Drehmomentschlüssel -V.A.G 1332/-
- Schraube M12 × 1,5 x 75
Ausbauen
- NZahnriemen von Nockenwelle und Hochdruckpumpe abnehmen
- Nockenwellenrad und die Nabe ausbauen
- Druckstück -3240/1- in die Nockenwelle einstecken.
- Innenteil des Dichtringausziehers 3240 2 Umdrehungen (ca. 3 mm) aus dem
Außenteil herausdrehen und mit Rändelschraube arretieren.
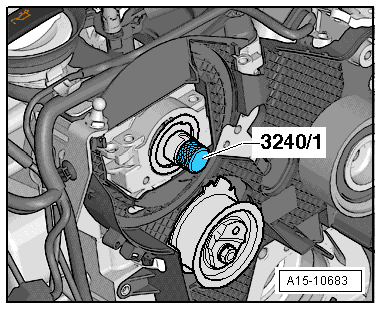
- Gewindekopf des Dichtringausziehers einölen, ansetzen und unter
kräftigem Druck so weit wie möglich in den Dichtring einschrauben.
- Rändelschraube lösen und Innenteil gegen die Nockenwelle drehen, bis der
Dichtring herausgezogen ist.
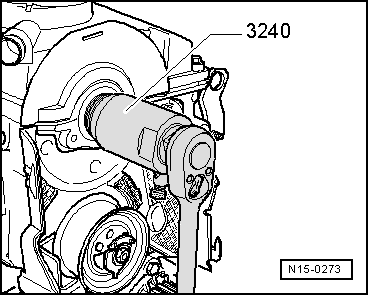
Einbauen
Hinweis
Die Dichtlippe des Dichtrings darf nicht zusätzlich eingeölt oder gefettet
werden.
- Ölrückstände am Nockenwellenzapfen mit einem sauberen Lappen entfernen.
- Führungshülse der Einziehvorrichtung -10 - 203- wie in der Abbildung
gezeigt auf die Nockenwelle aufstecken.
- Wellendichtring -1- vorsichtig über die
Führungshülse auf die Nockenwelle aufschieben.
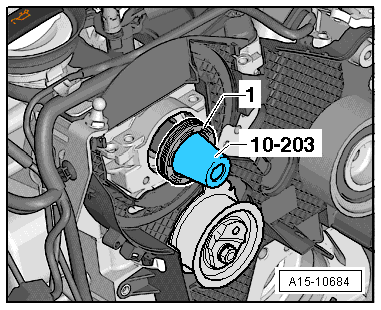
- Dichtring mit dem Druckstück der Einziehvorrichtung 10-203 und Schraube
M12×1,5×75 bis zum Anschlag einpressen.
- Nockenwellenrad und die Nabe einbauen.
- Zahnriemen einbauen und die Steuerzeiten einstellen.
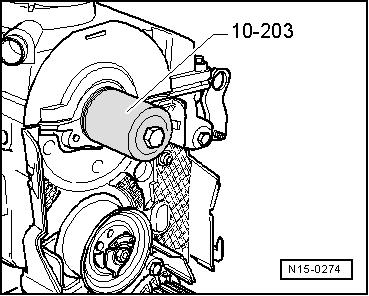
Fahrzeuge mit "neuem" Dichtring
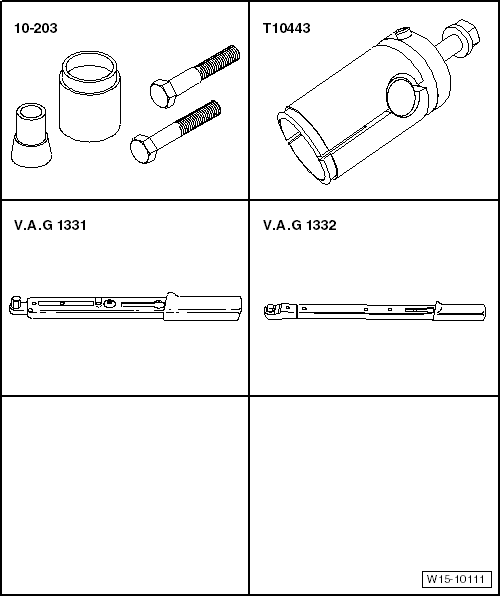
Benötigte Spezialwerkzeuge, Prüf- und Messgeräte sowie Hilfsmittel
- Einziehvorrichtung -V.A.G 10-203-
- Dichtringauszieher -T10443-
- Drehmomentschlüssel -V.A.G 1331/-
- Drehmomentschlüssel -V.A.G 1332/-
- Schraube M12 × 1,5 x 75
Ausbauen
- Zahnriemen von Nockenwelle und Hochdruckpumpe abnehmen.
- Nockenwellenrad und die Nabe ausbauen.
Vorsicht!
Bei zu weitem Zurückdrehen löst sich der innen liegende Druckteller von der
Druckschraube. In diesem Falle muss der Druckteller wieder auf die Druckschraube
gedrückt werden.
- Druckschraube des Dichtringausziehers "mit
Fingerspitzengefühl" zurückdrehen, bis ein leichter Widerstand zu
spüren ist.
Hinweis
Die Klemmhülsen des Dichtringausziehers sind mit Madenschrauben versehen. Nur
eine dieser Madenschrauben -Pfeil- führt jedoch die
Klemmung herbei, die andere ist fest verschraubt.
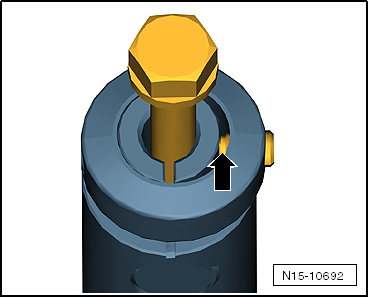
Einbauen
Hinweis
Die Dichtlippe des Dichtrings darf nicht zusätzlich eingeölt oder gefettet
werden.
- Ölrückstände am Nockenwellenzapfen mit einem sauberen Lappen entfernen.
- Führungshülse der Einziehvorrichtung -10 - 203- wie in der Abbildung
gezeigt auf die Nockenwelle aufstecken. Die Schrift auf dem Dichtring zeigt
nach außen.
- Wellendichtring -1- vorsichtig über die
Führungshülse auf die Nockenwelle aufschieben.
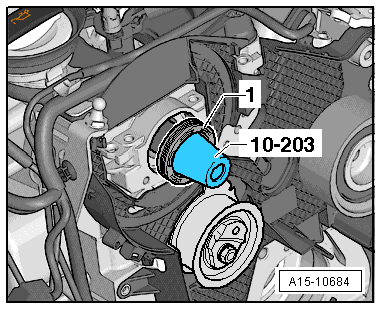
- Dichtring mit dem Druckstück der Einziehvorrichtung 10-203 und Schraube
M12×1,5×75 bis zum Anschlag einpressen.
- Nockenwellenrad und die Nabe einbauen.
- Zahnriemen einbauen und die Steuerzeiten einstellen.
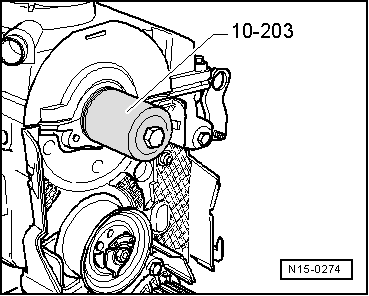
Hydraulische Ausgleichselemente prüfen
Hinweis
- Die hydraulischen Ausgleichselemente können nicht in Stand gesetzt
werden.
- Unregelmäßige Ventilgeräusche während des Anlassens sind normal.
Benötigte Spezialwerkzeuge, Prüf- und Messgeräte sowie Hilfsmittel
Arbeitsablauf
- Motor starten und so lange laufen lassen, bis der Kühlerlüfter einmal
eingeschaltet hat.
- Drehzahl für 2 Minuten auf etwa 2500/min erhöhen; wenn erforderlich,
Probefahrt durchführen.
Hinweis
Wenn die unregelmäßigen Ventilgeräusche verschwinden, aber im
Kurzstreckenverkehr immer wieder auftreten, muss das Ölrückhalteventil ersetzen
werden. Einbauort des Ölrückhalteventils im Ölfilterhalter.
Wenn die hydraulischen Ausgleichselemente noch laut sind, defektes
Ausgleichselement wie folgt ermitteln:
- Zylinderkopfhaube ausbauen.
- Kurbelwelle an der Schraube für Zahnriemenrad drehen, bis der Nocken des
zu prüfenden Ausgleichselements oben steht.
- Zum Ermitteln des Spiels zwischen Nocken und Rollenschlepphebel den
Rollenschlepphebel nach unten drücken -Pfeil-.
- Wenn sich eine Fühlerblattlehre 0,20 mm zwischen Nocken und
Rollenschlepphebel schieben lässt, hydraulisches Ausgleichselement wechseln.
Abschließende Maßnahmen
- Zylinderkopfhaube einbauen.
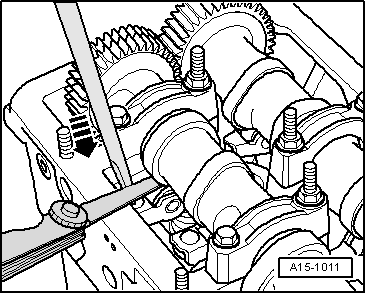
Ventilschaftabdichtungen aus- und einbauen
Ventilschaftabdichtungen bei eingebautem Zylinderkopf ersetzen
Benötigte Spezialwerkzeuge, Prüf- und Messgeräte sowie Hilfsmittel
- Abzieher für Ventilschaftabdichtung -3364-
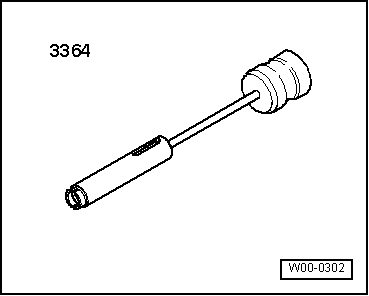
- Aufdrücker für Ventilschaftabdichtung -3365-
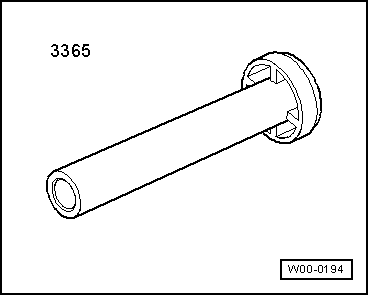
- De- und Montagevorrichtung für Ventilkegelstücke -VAS 5161- mit
Führungsplatte -VAS 5161/23- und Hülse -VAS 5161/23-1-
- 2x Schraube M6x30
Arbeitsablauf
- Alle Glühkerzen ausbauen.
- Nockenwellen ausbauen.
- Für den Wiedereinbau Zuordnung der Rollenschlepphebel und hydraulischen
Ausgleichselemente kennzeichnen.
- Rollenschlepphebel zusammen mit den hydraulischen Ausgleichselementen
herausnehmen und auf einer sauberen Unterlage ablegen.
- Kolben des jeweiligen Zylinders in den "unteren Totpunkt" stellen.
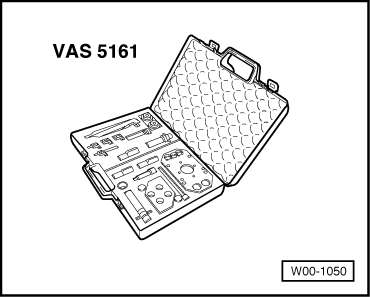
- Führungsplatte -VAS 5161/23- auf den Zylinderkopf aufsetzen.
- Führungsplatte an der Saugrohrseite mit der Rändelschraube -VAS 5161/12-
und 2 Schrauben M6x30 -Pos. 1- bis zur Anlage
von Hand festschrauben.
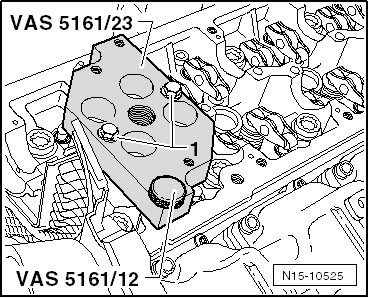
- Abdichtbolzen -VAS 5161/10- in die Führungsplatte einschrauben.
- Adapter -VAS 5161/11- handfest in das jeweilige Glühstiftkerzengewinde
einschrauben.
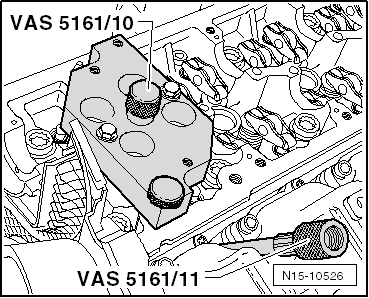
- Schlagdorn -VAS 5161/3- in die Führungsplatte einsetzen und festsitzende
Ventilkegelstücke mit einem Kunststoffhammer losschlagen.
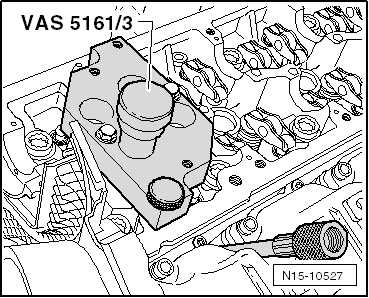
- Rasterteil -VAS 5161/6- mit Einhängegabel -VAS 5161/5- in die
Führungsplatte einschrauben.
- Hülse -VAS 5161/23-1- auf die Montagepatrone -VAS 5161/8- aufschieben.
- Adapter über ein handelsübliches Zwischenstück an Druckluft anschließen
und ständig Druck geben.
- Mindestdruck: 6 bar Überdruck.
- Druckgabel -VAS 5161/2- am Rasterteil einhängen und Montagepatrone nach
unten drücken.
- Gleichzeitig Rändelschraube der Montagepatrone nach rechts drehen, bis
die Spitzen in die Ventilkegelstücke einrasten.
- Rändelschraube links- und rechtsdrehend bewegen, dadurch werden die
Ventilkegelstücke auseinandergedrückt und in die Montagepatrone aufgenommen.
- Druckgabel loslassen.
- Montagepatrone mit Rändel-Abstandsring abnehmen.
- Ventilfeder mit Ventilfederteller abnehmen.
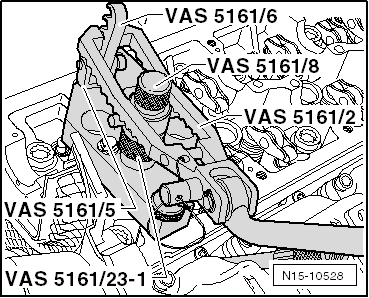
- Ventilschaftabdichtung mit dem Abzieher für Ventilschaftabdichtung
-3364- abziehen.

Vorsicht!
Beschädigungsgefahr beim Einbau der Ventilschaftabdichtungen.
Kunststoffhülse -A-, die neuen
Ventilschaftabdichtungen -B- beigefügt ist, auf den
Ventilschaft stecken.
- Dichtlippe der Ventilschaftabdichtung leicht einölen.
- Ventilschaftabdichtung auf die Kunststoffhülse aufschieben.
- Ventilschaftabdichtung mit dem Aufdrücker für Ventilschaftabdichtung
-3365- vorsichtig auf die Ventilführung aufdrücken.
- Kunststoffhülse abnehmen.
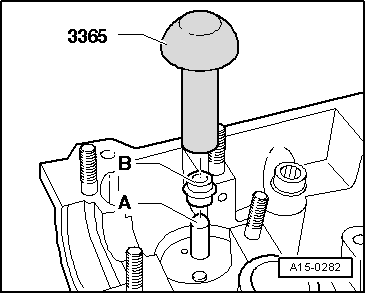
Wenn die Ventilkegelstücke aus der Montagepatrone genommen wurden, zunächst
in die Ventileinlegevorrichtung -VAS 5161/18- einsetzen.
- Der große Durchmesser der Ventilkegelstücke zeigt nach oben.
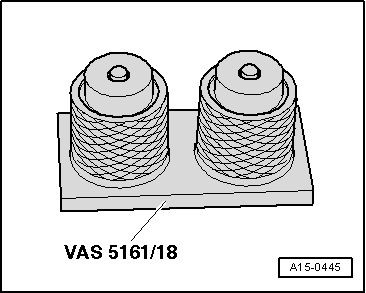
- Ventilfeder und Ventilfederteller einsetzen.
- Montagepatrone von oben auf die Einlegevorrichtung für Ventilkegelstücke
aufdrücken und Ventilkegelstücke aufnehmen.
- Montagepatrone wieder in die Führungsplatte -VAS 5161/23- einsetzen.
- Druckgabel niederdrücken und Rändelschraube links- und rechtsdrehend
nach oben ziehen, dadurch werden die Ventilkegelstücke eingesetzt.
- Druckgabel bei noch gezogener Rändelschraube entlasten.
- Vorgang an jedem Ventil wiederholen.
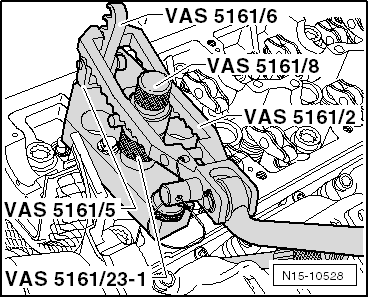
Zusammenbauen
Der Zusammenbau erfolgt in umgekehrter Reihenfolge, dabei Folgendes beachten:
- Darauf achten, dass alle Rollenschlepphebel richtig auf den
Ventilschaftenden aufliegen und auf den jeweiligen hydraulischen
Ausgleichselementen eingeclipst sind.
- Nockenwellen einbauen.
- Glühkerzen einbauen.
Ventilschaftabdichtungen bei ausgebautem Zylinderkopf ersetzen
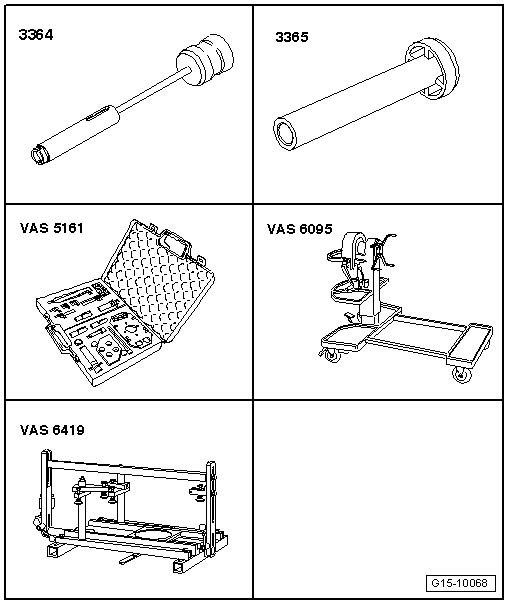
Benötigte Spezialwerkzeuge, Prüf- und Messgeräte sowie Hilfsmittel
- Abzieher für Ventilschaftabdichtung -3364-
- Aufdrücker für Ventilschaftabdichtung -3365-
- De- und Montagevorrichtung für Ventilkegelstücke -VAS 5161- mit
Führungsplatte -VAS 5161/23- und Hülse -VAS 5161/23-1-
- Motor- und Getriebehalter -VAS 6095-
- Zylinderkopfaufspannvorrichtung -VAS 6419-
- 2x Schraube M6x30
Arbeitsablauf
- Nockenwellen ausbauen.
- Für den Wiedereinbau Zuordnung der Rollenschlepphebel und hydraulischen
Ausgleichselemente kennzeichnen.
- Rollenschlepphebel zusammen mit den hydraulischen Ausgleichselementen
herausnehmen und auf einer sauberen Unterlage ablegen.
- Zylinderkopfaufspannvorrichtung -VAS 6419- in den Motor- und
Getriebehalter -VAS 6095- einsetzen.
- Zylinderkopf auf die Zylinderkopfaufspannvorrichtung aufspannen, wie in
der Abbildung gezeigt.
- Zylinderkopfaufspannvorrichtung an Druckluft anschließen.
- Luftkissen mit dem Hebel -Pfeil- unter
denjenigen Verbrennungsraum schieben, an dem die Ventilschaftabdichtung
ausgebaut werden soll.
- Gerade so viel Druckluft in das Luftkissen einströmen lassen, bis es
sich an die Ventilteller anlegt.
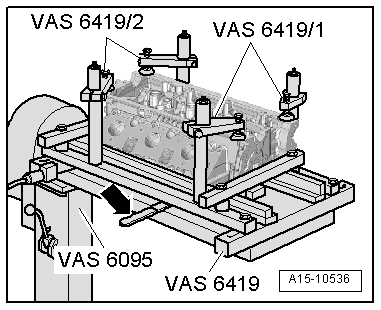
- Führungsplatte -VAS 5161/23- auf den Zylinderkopf aufsetzen.
- Führungsplatte an der Saugrohrseite mit der Rändelschraube -VAS 5161/12-
und 2 Schrauben M6x30 -Pos. 1- bis zur Anlage
von Hand festschrauben.
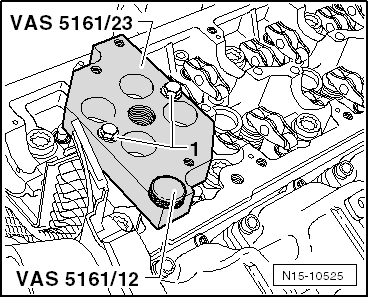
- Schlagdorn -VAS 5161/3- in die Führungsplatte einsetzen und festsitzende
Ventilkegelstücke mit einem Kunststoffhammer losschlagen.
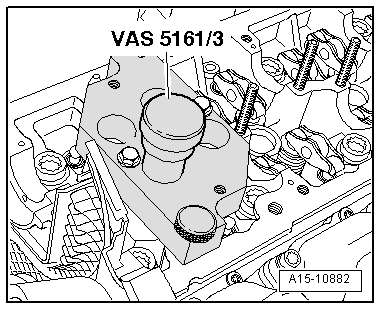
- Rasterteil -VAS 5161/6- mit Einhängegabel -VAS 5161/5- in die
Führungsplatte einschrauben.
- Hülse -VAS 5161/23-1- auf die Montagepatrone -VAS 5161/8- aufschieben.
- Druckgabel -VAS 5161/2- am Rasterteil einhängen und Montagepatrone nach
unten drücken.
- Gleichzeitig Rändelschraube der Montagepatrone nach rechts drehen, bis
die Spitzen in die Ventilkegelstücke einrasten.
- Rändelschraube links- und rechtsdrehend bewegen, dadurch werden die
Ventilkegelstücke auseinandergedrückt und in die Montagepatrone aufgenommen.
- Druckgabel loslassen.
- Montagepatrone mit Rändel-Abstandsring abnehmen.
- Ventilfeder mit Ventilfederteller abnehmen.
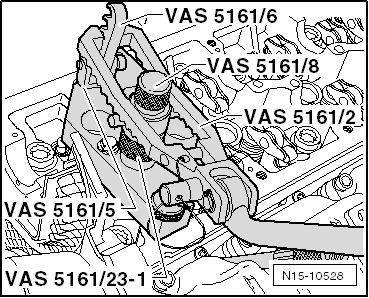
- Ventilschaftabdichtung mit dem Abzieher für Ventilschaftabdichtung
-3364- abziehen.
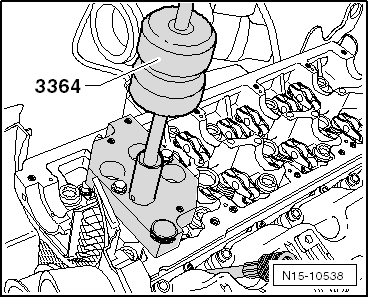
Vorsicht!
Beschädigungsgefahr beim Einbau der Ventilschaftabdichtungen.
Kunststoffhülse -A-, die neuen
Ventilschaftabdichtungen -B- beigefügt ist, auf den
Ventilschaft stecken.
- Dichtlippe der Ventilschaftabdichtung leicht einölen.
- Ventilschaftabdichtung auf die Kunststoffhülse aufschieben.
- Ventilschaftabdichtung mit dem Aufdrücker für Ventilschaftabdichtung
-3365- vorsichtig auf die Ventilführung aufdrücken.
- Kunststoffhülse abnehmen.
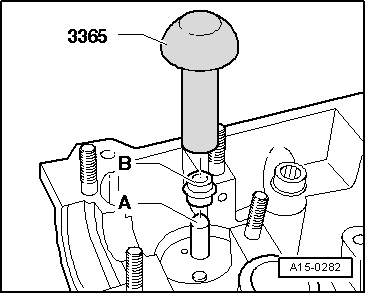
Wenn die Ventilkegelstücke aus der Montagepatrone genommen wurden, zunächst
in die Ventileinlegevorrichtung -VAS 5161/18- einsetzen.
- Der große Durchmesser der Ventilkegelstücke zeigt nach oben.
- Ventilfeder und Ventilfederteller einsetzen.
- Montagepatrone von oben auf die Einlegevorrichtung für Ventilkegelstücke
aufdrücken und Ventilkegelstücke aufnehmen.
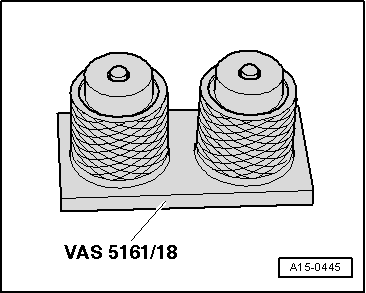
- Montagepatrone wieder in die Führungsplatte -VAS 5161/23- einsetzen.
- Druckgabel niederdrücken und Rändelschraube links- und rechtsdrehend
nach oben ziehen, dadurch werden die Ventilkegelstücke eingesetzt.
- Druckgabel bei noch gezogener Rändelschraube entlasten.
- Vorgang an jedem Ventil wiederholen.
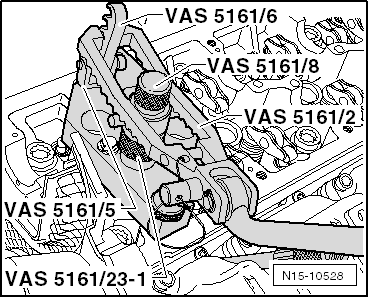
Zusammenbauen
Der Zusammenbau erfolgt in umgekehrter Reihenfolge, dabei Folgendes beachten:
- Darauf achten, dass alle Rollenschlepphebel richtig auf den
Ventilschaftenden aufliegen und auf den jeweiligen hydraulischen
Ausgleichselementen eingeclipst sind.
- Nockenwellen einbauen.
Montageübersicht - Zahnriemen
Zahnriemen
vor Ausbau Laufrichtung kennzeichnen
auf Verschleiß prüfen
nicht knicken
aus- und einbauen, spannen
120 Nm + 90º ...
Ventilmaße
Hinweis
Ein- und Auslassventile dürfen nicht nachgearbeitet werden. Nur das
Einschleifen ist zulässig.
Maß
Einlassventil
Auslassventil
Ø a
mm
2 ...