Volkswagen Tiguan Reparaturanleitung: Zylinderkopf
Montageübersicht - Zylinderkopf
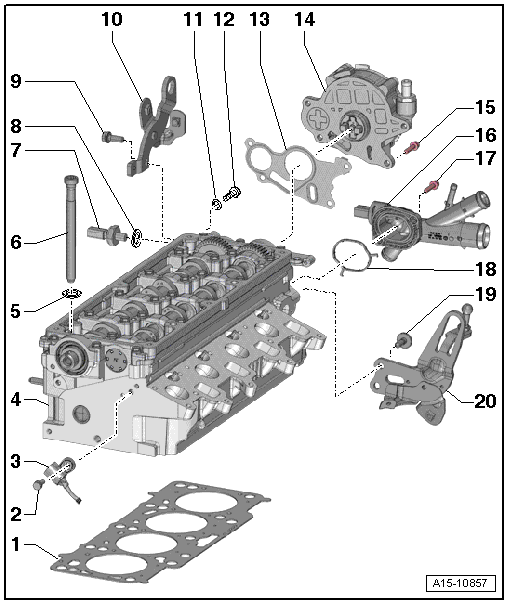
- Zylinderkopfdichtung
- ersetzen
- Kennzeichnung Zylinderkopfdichtung
- nach dem Ersetzen Kühlmittel und Motoröl wechseln
- 10 Nm
- mit Sicherungsmittel einsetzen; Sicherungsmittel
- Hallgeber -G40-
- für Nockenwellenposition
- aus- und einbauen
- Zylinderkopf
- aus- und einbauen
- ausgebauten Zylinderkopf nur auf einer Schaumstoffunterlage ablegen,
da andernfalls die Glühkerzen beschädigt werden können
- auf Verzug prüfen
- darf nicht nachgearbeitet werden
- vor dem Einbauen kontrollieren, ob beide Passhülsen zur Zentrierung
des Zylinderkopfs am Zylinderblock vorhanden sind
- nach dem Ersetzen Kühlmittel und Motoröl wechseln
- Unterlegscheibe
- Zylinderkopfschraube
- ersetzen
- Reihenfolge beim Lösen
- Anzugsdrehmoment und -reihenfolge
- Öldruckschalter -F1-, 20 Nm
- Schaltdruck 0,3 ... 0,6 bar
- aus- und einbauen
- prüfen
- Dichtring
- 20 Nm
- Motoraufhängeöse
- Dichtring
- 20 Nm
- Dichtung
- Unterdruckpumpe
- 10 Nm
- Anschlussstutzen
- für Kühlmittelschläuche
- mit Kühlmitteltemperaturgeber -G62-
- 9 Nm
- Dichtung
- 20 Nm
- Motoraufhängeöse
Reihenfolge beim Lösen der Zylinderkopfschrauben
- Schrauben für Zylinderkopf in der Reihenfolge
-1... 10- lösen.
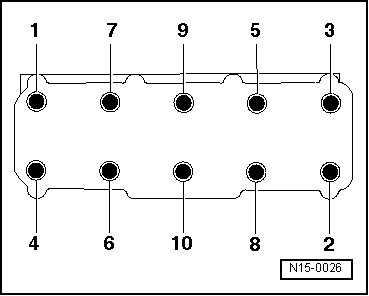
Zylinderkopf auf Verzug prüfen
- Zylinderkopf mit Haarlineal und Fühlerblattlehre an mehreren Stellen auf
Verzug prüfen.
- Maximal zulässiger Verzug: 0,1 mm.
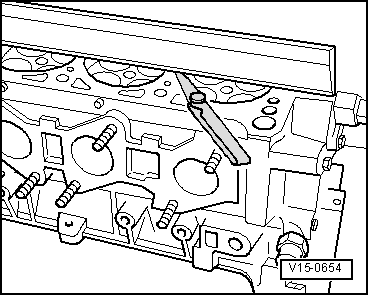
Hinweis
Zylinderköpfe für TDI-Motoren dürfen nicht nachgearbeitet werden.
Kennzeichnung Zylinderkopfdichtung
- Teilenummer
- Löcher
- nicht beachten
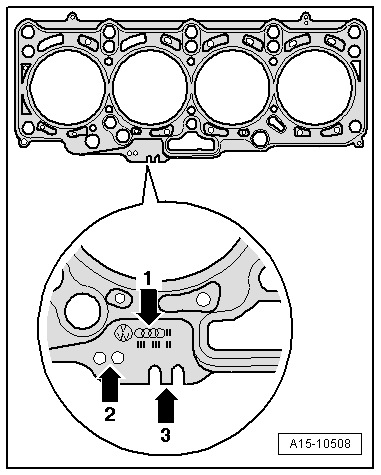
Hinweis
Je nach Kolbenüberstand werden in der Dicke unterschiedliche
Zylinderkopfdichtungen eingebaut. Wird nur die Zylinderkopfdichtung ersetzt,
eine neue Zylinderkopfdichtung gleicher Kennzeichnung einbauen.
Zylinderkopf - Anzugsdrehmoment und -reihenfolge
Hinweis
Schrauben für Zylinderkopf ersetzen.
- Schrauben in 4 Stufen in der gezeigten Reihenfolge festziehen:
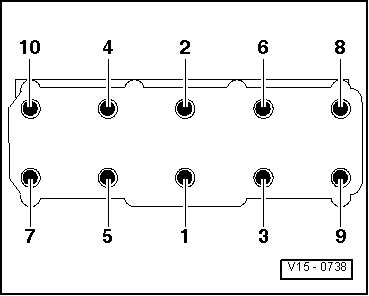
Zylinderkopf aus- und einbauen
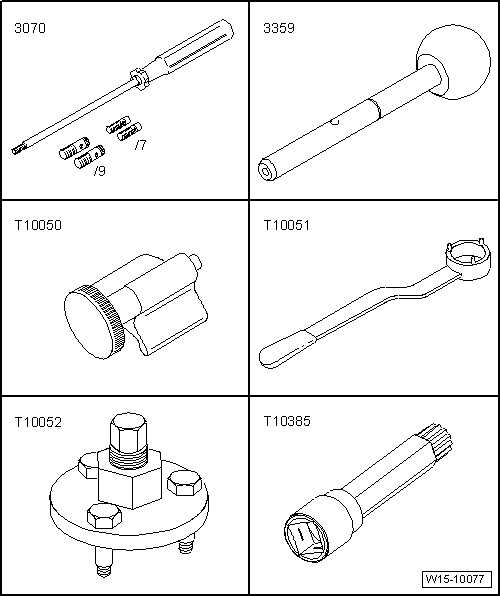
Benötigte Spezialwerkzeuge, Prüf- und Messgeräte sowie Hilfsmittel
- Führungsbolzen -3070-
- Absteckstift für Diesel-Einspritzpumpe -3359-
- Kurbelwellenstopp -T10050-
- Gegenhalter -T10051-
- Abziehvorrichtung -T10052-
- Steckeinsatz XZN 10 -T10385-
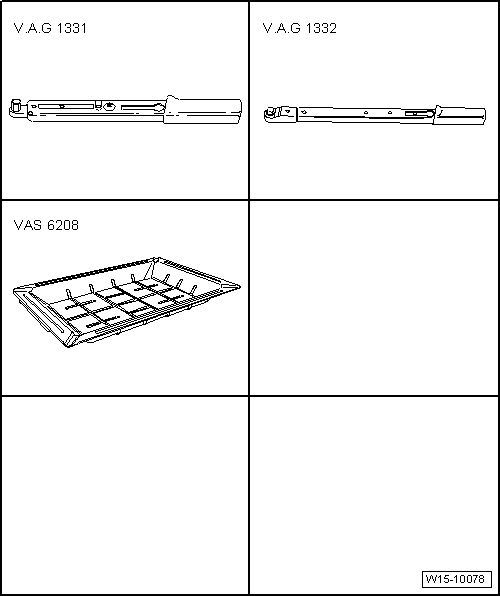
- Drehmomentschlüssel -V.A.G 1331-
- Drehmomentschlüssel -V.A.G 1332-
- Auffangwanne für Werkstattkräne -VAS 6208-
Hinweis
- Anti-Diebstahl-Codierung des Radios erfragen, da im weiteren
Arbeitsablauf das Masseband der Batterie abgeklemmt werden muss.
- Alle Kabelbinder, die beim Zylinderkopfausbau gelöst oder aufgeschnitten
werden, müssen beim Zylinderkopfeinbau an der gleichen Stelle wieder
befestigt werden.
ACHTUNG!
Bei allen Montagearbeiten, insbesondere im Motorraum auf Grund der engen
Bauverhältnisse, bitte Folgendes beachten:
- Leitungen aller Art so verlegen, dass die ursprüngliche Leitungsführung
wiederhergestellt werden kann.
- Auf ausreichenden Freigang zu allen beweglichen oder heißen Bauteilen
achten.
Ausbauen
- Masseband an der Batterie bei ausgeschalteter Zündung abklemmen.
- Motorabdeckung abbauen.
- Luftfiltergehäuse ausbauen.
- Batterie und den Batterieträger ausbauen
- Luftführungshutze mit Kühlerlüfter -V7- und Kühlerlüfter rechts -V35-
ausbauen
- Verbindungsschlauch "kalte Seite" am
Ladeluftkühler ausbauen.
- Zylinderkopfhaube ausbauen.
- Steckverbindung von der Drosselklappensteuereinheit -J338--2-
abziehen.
- Schraube von der Ölmessstabanbindung -4-
herausdrehen.
- Unterdruckleitung von der Unterdruckpumpe abziehen.
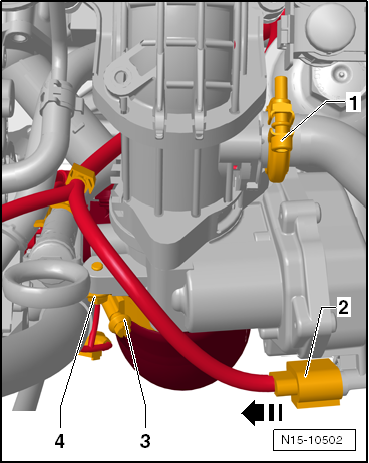
- Schrauben -2, 5- und
-Pfeile- herausdrehen.
- Elektrische Leitungen und Schläuche mit Abdrückhebel -80 - 200- am
Luftführungsrohr links frei legen.
- Schlauchschelle -3- lösen und das
Luftführungsrohr links abnehmen.
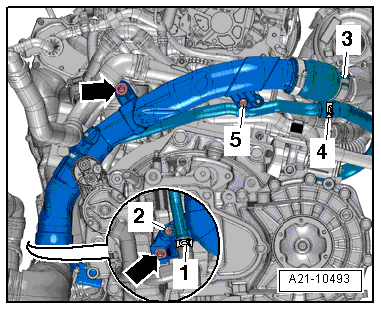
- Schrauben -Pfeile- herausdrehen und den
Pulsationsdämpfer -2- abnehmen.
- Geräuschdämpfung ausbauen
- Kühlmittel ablassen
- Die elektrische Steckverbindung -4- am
Kühlmitteltemperaturgeber -G62- trennen.
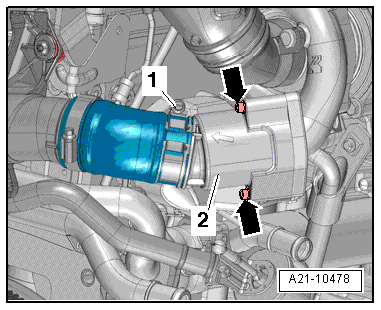
- Kühlmittelschläuche vom Anschlussstutzen abziehen. Dazu Schlauchschellen
-1- und -2- lösen.
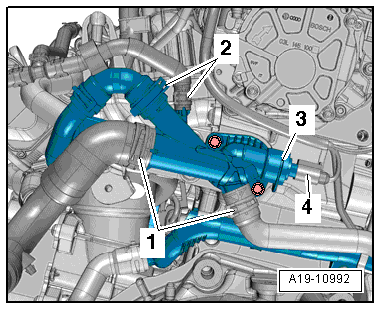
- Die elektrische Steckverbindung -1- am
Öldruckschalter -F1- trennen.
- Schraube -Pfeil- herausdrehen.
- Unterdruckschlauch -2- abziehen.
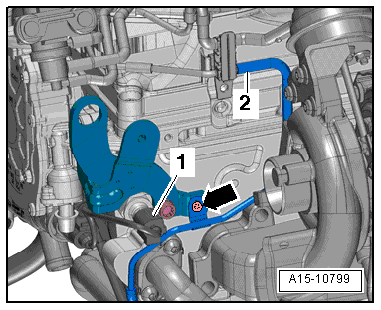
- Elektrische Steckverbindung -3- aus dem
Halter nehmen und trennen.
- Elektrische Leitungen am Abgasturbolader frei legen.
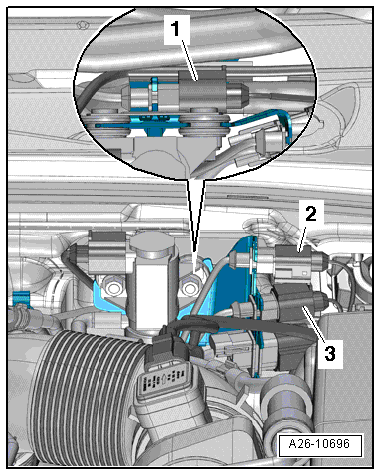
- Befestigungsschrauben -Pfeile- vom
Ladeluftrohr herausnehmen und die Steckverbindung vom Ladedruckgeber -G31--1-
trennen.
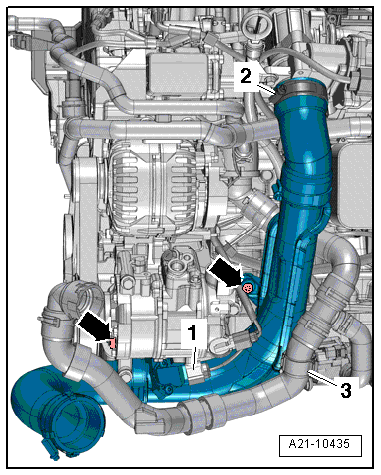
- Schelle -2- öffnen, den Kühlmittelschlauch
-3- freilegen und das Ladeluftrohr abnehmen.
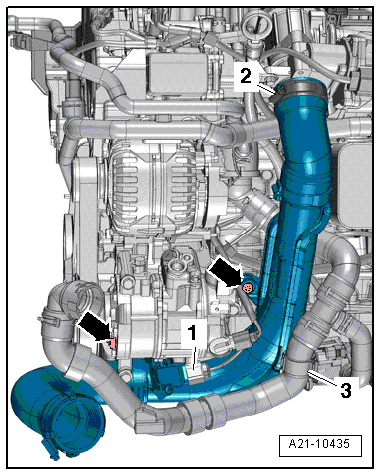
Vorsicht!
Darauf achten, dass das Entkopplungselement des Verbindungsrohrs nicht
gebogen und somit überdehnt wird. Es besteht die Gefahr der Rissbildung.
- Verbindungsrohre für Abgasrückführung -A-
mit dem Steckeinsatz -T10385- ausbauen.

- Befestigungsmuttern -Pfeile- des Halters
für Partikelfilter -A- am Kurbelgehäuse
abschrauben.
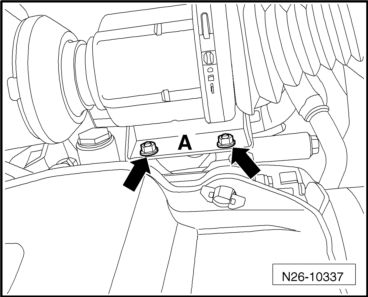
- Überwurfmutter -2- abschrauben und die
Schraube -3- herausdrehen.
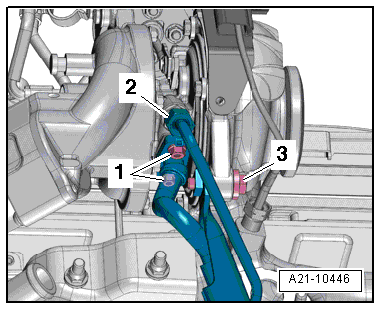
- Schraube -Pfeil- am Zahnriemenschutz hinten
herausdrehen.
- Verbindungsschelle zwischen Abgasturbolader und Partikelfilter lösen.
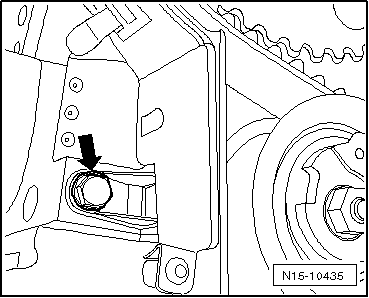
- Befestigungsschraube vom Halter am Zylinderkopf
-Pfeil- abdrehen und den Partikelfilter zur Seite drücken.
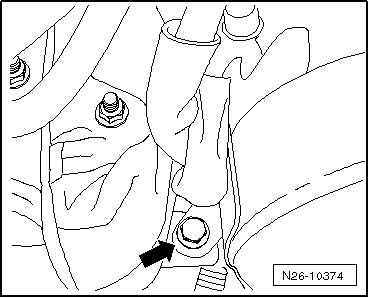
- Steckverbindung für Hallgeber -G40--Pfeil-
abziehen.
- Zahnriemen von der Nockenwelle abnehmen
- Zahnriemenrad der Nockenwelle abbauen und die Nabe der Nockenwelle mit
der Abziehvorrichtung -T10052- abziehen.
- Befestigungsmutter der Zahnriemenspannrolle abschrauben.
- Reihenfolge -1 ... 10- beim Lösen der
Zylinderkopfschrauben einhalten.
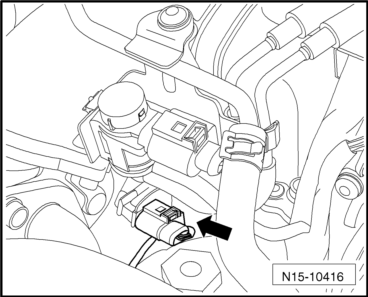
Hinweis
- Zum Herausnehmen des Zylinderkopfs ist ein zweiter Mechaniker
erforderlich.
- Die Zahnriemenspannrolle wird beim Herausheben des Zylinderkopfs von
der Stiftschraube gezogen.
- Die Ölrücklaufleitung des Abgasturboladers wird beim Herausheben des
Zylinderkopfs aus der Stütze gezogen.
- Zylinderkopf zuerst getriebeseitig anheben und aus dem Zahnriemenschutz
herausfädeln. Darauf achten, dass die Zahnriemenspannrolle nicht
herunterfällt.
- Zylinderkopf so ablegen, dass sich die Ölrücklaufleitung nicht verbiegt.
Holzstück unter den Abgaskrümmer legen.
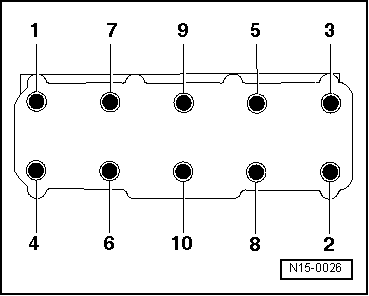
Einbauen
Hinweis
- Zylinderkopfschrauben immer ersetzen.
- Dichtmittelreste im Reparaturfall von Zylinderkopf und Zylinderblock
vorsichtig entfernen. Darauf achten, dass keine lang gezogenen Riefen
oder Kratzer entstehen. Bei Verwendung von Schleifpapier darf die
Körnung nicht unter 100 liegen.
- Schmiergel- und Schleifreste sorgfältig entfernen.
- Neue Zylinderkopfdichtung erst unmittelbar vor dem Einbau aus der
Verpackung nehmen.
- Dichtung äußerst sorgfältig behandeln. Beschädigungen der
Siliconschicht und im Sickenbereich führen zu Undichtigkeiten.
- Vor dem Aufsetzen des Zylinderkopfs Kurbelwellenstopp -T10050- entfernen
und Kurbelwelle entgegen der Motordrehrichtung zurückdrehen, bis alle Kolben
nahezu gleichmäßig unter oberen Totpunkt stehen.
- Zylinderkopfdichtung mit der Kennzeichnung nach oben auflegen.
- Zum Zentrieren Führungsbolzen -3070- in die äußeren Bohrungen auf der
Ansaugseite einschrauben.
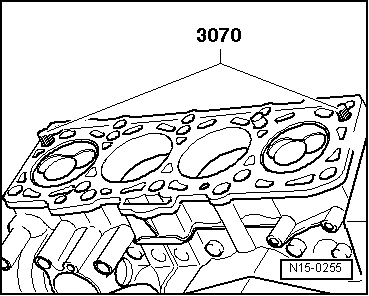
Hinweis
Die Spannrolle muss beim Aufsetzen des Zylinderkopfs auf die Stiftschraube
gesteckt werden.
- Zylinderkopf aufsetzen, 8 Zylinderkopfschrauben einsetzen und handfest
anziehen.
- Führungsbolzen mit Bolzendreher aus 3070 durch die Schraubenbohrungen
herausschrauben und Zylinderkopfschrauben einsetzen.
- Zylinderkopf in 4 Stufen in gezeigter Anzugsreihenfolge wie folgt
anziehen:
- Mit Drehmomentschlüssel vorziehen:
- Stufe I = 30 Nm
- Stufe II = 50 Nm
- Mit starrem Schlüssel weiterdrehen:
- Stufe III = 90º
- Stufe IV = 90º
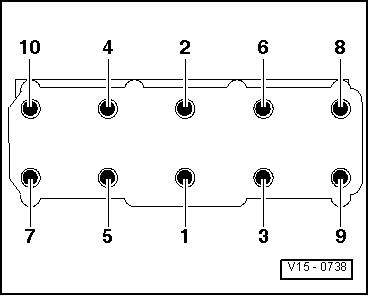
- Zahnriemenschutz hinten am Zylinderkopf befestigen.
- Nabe und das Nockenwellenrad einbauen.
- Nockenwelle und die Hochdruckpumpe mit dem Absteckstift für
Diesel-Einspritzpumpe -3359- arretieren.
- Kurbelwelle in Motordrehrichtung auf oberen Totpunkt drehen und die
Kurbelwelle mit dem Kurbelwellenstopp -T10050- arretieren.
- Zahnriemen auflegen.
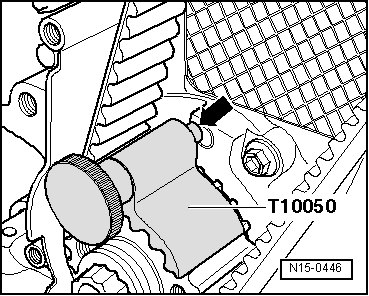
Der weitere Einbau erfolgt in umgekehrter Reihenfolge. Dabei ist Folgendes zu
beachten:
- Zylinderkopfhaube einbauen.
- Keilrippenriemen einbauen.
- Kühlmittel auffüllen.
- Probefahrt machen und den Ereignisspeicher abfragen.
Zylinderkopfhaube aus- und einbauen
Zylinderkopfhaube aus- und einbauen
Ausbauen
- Motorabdeckung ausbauen.
- Elektrische Steckverbindung -2- am
Differenzdruckgeber -G505- trennen.
- Schraube -3- herausdrehen,
Differenzdruckgeber -G505- vom Halter abziehen -Pfeil-
und zur Seite legen.
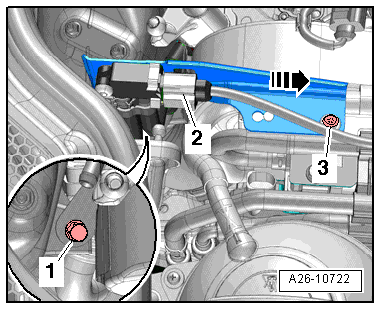
- Klammern -Pfeile- lösen und
Zahnriemenschutz oben nach rechts zur Seite drücken.
- Einspritzeinheiten und Kraftstoffverteiler ausbauen.
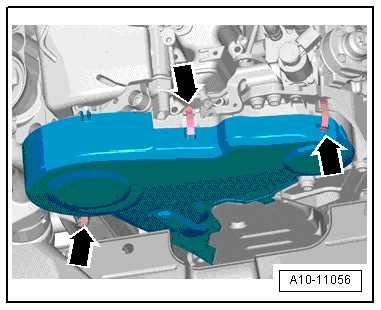
- Schlauch -1- für Kurbelgehäuseentlüftung
von der Zylinderkopfhaube abbauen, dazu Entriegelungstasten drücken.
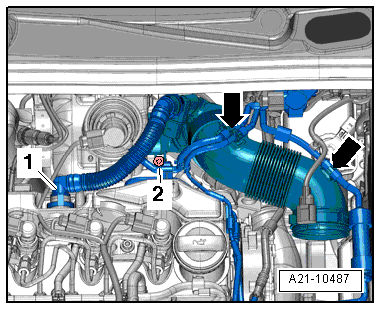
- Elektrische Steckverbindung -Pfeil- am
Positionsgeber für Ladedrucksteller -G581- trennen.
- Unterdruckleitungen aus dem Halter an der Zylinderkopfhaube nehmen.
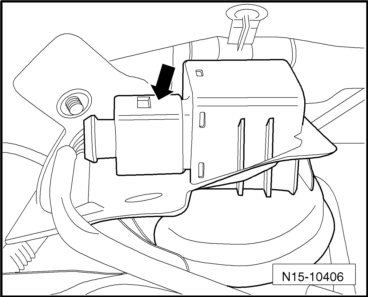
- Schrauben für Zylinderkopfhaube in der Reihenfolge
-6 ... 1- lösen und herausdrehen.
- Zylinderkopfhaube abnehmen.
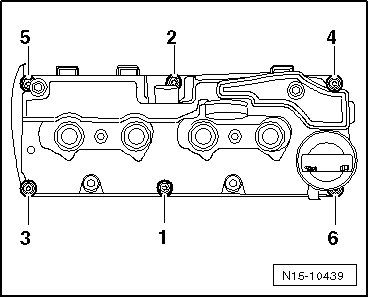
Einbauen
Der Einbau erfolgt in umgekehrter Reihenfolge, dabei Folgendes beachten:
Hinweis
- Dichtung für Zylinderkopfhaube und die Schrauben für Zylinderkopfhaube
bei Beschädigung oder Undichtigkeit ersetzen.
- Tüllen und Dichtringe für Injektoren bei Beschädigung oder Undichtigkeit
ersetzen.
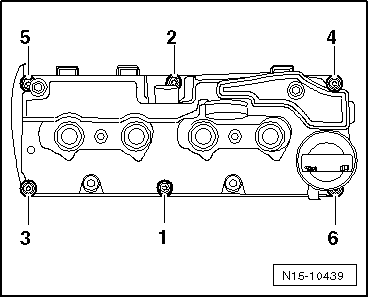
- Schrauben für Zylinderkopfhaube festziehen
- Darauf achten, dass die Zylinderkopfhaube korrekt mit dem
Zahnriemenschutz verclipst ist -Pfeile-
Hinweis
Einbaulage ist bei ausgebautem Nockenwellenrad dargestellt.
- Freigang zwischen der Nabe und dem Zahnriemenschutz prüfen.
- Kühlmittelrücklaufleitung einbauen.
- Ansaugstutzen einbauen.
- Kraftstoffverteiler und Einspritzeinheiten einbauen.
- Differenzdruckgeber -G505- einbauen.
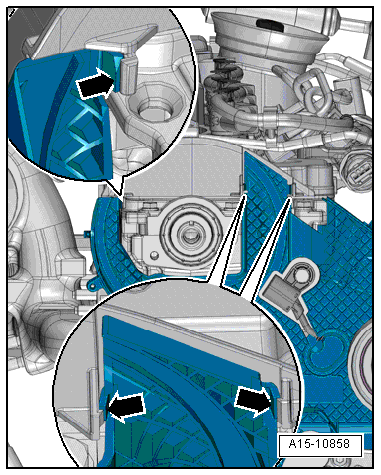
Dichtringe für Einspritzeinheiten ersetzen
Benötigte Spezialwerkzeuge, Prüf- und Messgeräte sowie Hilfsmittel
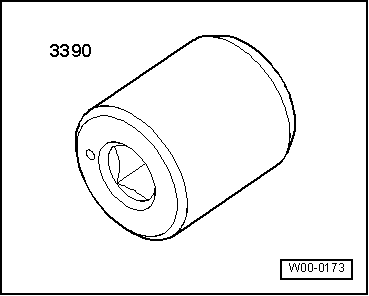
Arbeitsablauf
- Zylinderkopfhaube ausbauen
- Dichtring für Einspritzeinheit mit Mitnehmer -3390- und kurzer
Verlängerung -1- von unten nach oben ausdrücken
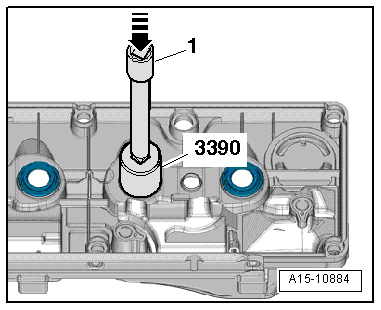
- Neuen Dichtring für Einspritzeinheit mit Mitnehmer -3390- und kurzer
Verlängerung -1- von oben bis zum Anschlag
einpressen.
- Zylinderkopfhaube einbauen.
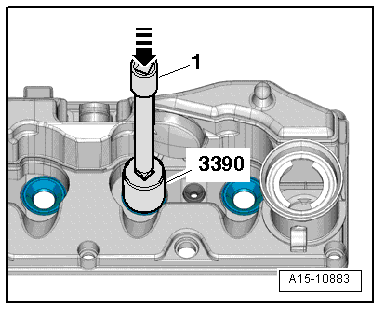
Montageübersicht - Zylinderkopfhaube
Vorsicht!
Beim Einbau eines neuen Rumpfmotors ist es zwingend erforderlich, nach
Montage der Hochdruckleitungen die Spannpratzen der Einspritzeinheiten mit
vorgeschriebenem Drehmoment festzuziehen. Zur Ausrichtung der Einspritzeinheiten bei Montage der
Hochdruckleitungen sind die Spannpratzen nach Auslieferung nur
"handfest" angezogen. Bei Nichtbeachtung kann es zu
Motorschäden kommen.
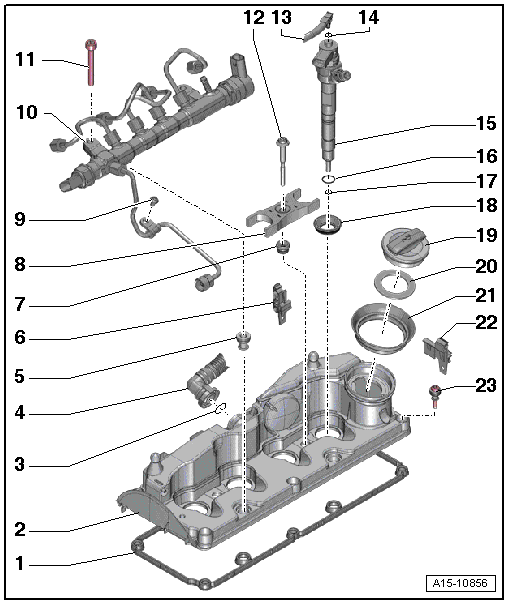
- Dichtung
- bei Beschädigung oder Undichtigkeit ersetzen
- Zylinderkopfhaube
- O-Ring
- Schlauch
- für Kurbelgehäuseentlüftung
- zum Abbauen Entriegelungstasten drücken
- Dichtbuchse
- für Kraftstoffverteiler
- bei Beschädigung oder Undichtigkeit ersetzen
- Halter
- für elektrische Leitungen
- Tülle
- Spannpratze
- 8 Nm
- Hochdruckspeicher (Rail)
- Sauberkeitsregeln beachten
- Biegeform der Hochdruckleitungen nicht verändern
- Hochdruckleitungen einbauen
- 22 Nm
- 8 Nm + 180º weiterdrehen
- Kraftstoffrücklaufleitung
- O-Ring
- Einspritzeinheit
- Sauberkeitsregeln beachten
- aus- und einbauen
- O-Ring
- Wärmeschutzdichtung
- Dichtring
- für Einspritzeinheit
- ersetzen
- Verschlussdeckel
- Dichtung
- Tülle
- Halter
- für elektrische Leitungen
- Schraube
- bei beschädigter Dichtung ersetzen
- Anzugsdrehmoment und -reihenfolge
Zylinderkopfhaube - Anzugsdrehmoment und -reihenfolge
- Schrauben für Zylinderkopfhaube in der Reihenfolge
-1 ... 6- mit 9 Nm festziehen.
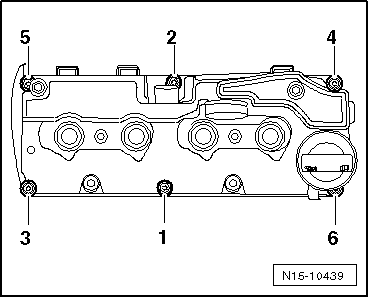
Unterdruckpumpe aus- und einbauen
GEFAHR!
Die Unterdruckpumpe darf unter keinen Umständen zerlegt werden, da es
ansonsten zur Fehlfunktion des Vakuumteils kommen kann. Die Folge wäre ein
Ausfall des Bremskraftverstärkers.
Ausbauen
- Luftfiltergehäuse ausbauen.
- Unterdruckleitung -1- von der
Unterdruckpumpe -2- abziehen.
- Befestigungsschrauben des Ladeluftrohrs herausschrauben.
- Ladeluftrohr etwas nach unten drücken, um die hintere Verschraubung der
Unterdruckpumpe zu erreichen.
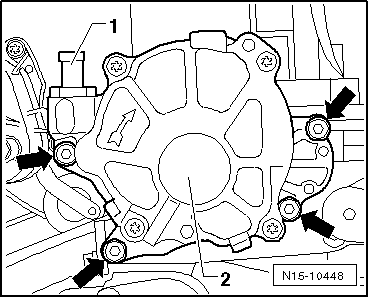
- Befestigungsschrauben -Pfeile-
herausdrehen.
- Unterdruckpumpe -2- vom Zylinderkopf
abnehmen.
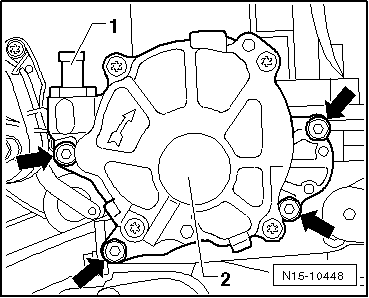
Einbauen
Der Einbau erfolgt in umgekehrter Reihenfolge, dabei ist Folgendes zu
beachten:
Hinweis
- Auf richtigen Sitz von der Kupplung der Unterdruckpumpe in der
Nockenwelle achten.
- Die Dichtung ist zu ersetzen.
- Unterdruckpumpe einbauen und die Befestigungsschrauben mit 10 Nm
festziehen.
- Unterdruckleitung -1- vom
Bremskraftverstärker an der Unterdruckpumpe anschließen.
Kompressionsdruck prüfen
Benötigte Spezialwerkzeuge, Prüf- und Messgeräte sowie Hilfsmittel
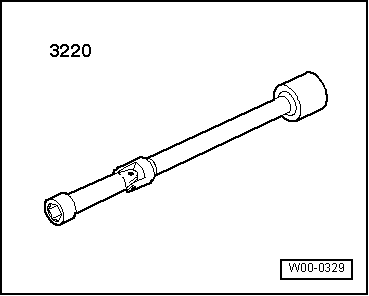
- Kompressionsdruck-Prüfgerät -V.A.G 1763- mit Adapter -V.A.G 1763/8-
- Drehmomentschlüssel (5 ... 50 Nm) -V.A.G 1331-
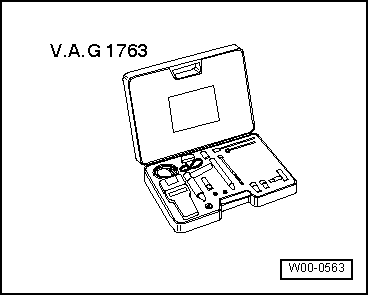
Prüfbedingung
- Motoröltemperatur mind. 30 ºC
Prüfablauf
- Steckverbindungen an den Einspritzeinheiten abziehen.
- Glühstiftkerzen mit dem Gelenkschlüssel -3220- ausbauen.
- Adapter -V.A.G 1763/8- anstelle der Glühstiftkerze einschrauben.
- Kompressionsdruck mit Kompressionsdruck-Prüfgerät -V.A.G 1763- prüfen.
Hinweis
Handhabung des Prüfgeräts ⇒ Bedienungsanleitung.
- Motor so lange starten, bis kein Druckanstieg mehr vom Prüfgerät
angezeigt wird.
Kompressionsdruckwerte:
Neu: 25 ... 31 bar Überdruck
Verschleißgrenze: 19 bar Überdruck
Zulässiger Unterschied zwischen sämtlichen Zylindern: 5 bar
- Glühstiftkerze mit dem Gelenkschlüssel -3220- einbauen
- Ereignisspeicher des Motorsteuergeräts abfragen
Hinweis
Durch das Trennen der Steckverbindungen für Einspritzeinheiten werden
Ereignisse im Ereignisspeicher abgespeichert. Daher Ereignisspeicher abfragen
und ggf. löschen.
Montageübersicht - Zahnriemen
Zahnriemen
vor Ausbau Laufrichtung kennzeichnen
auf Verschleiß prüfen
nicht knicken
aus- und einbauen, spannen
120 Nm + 90º ...